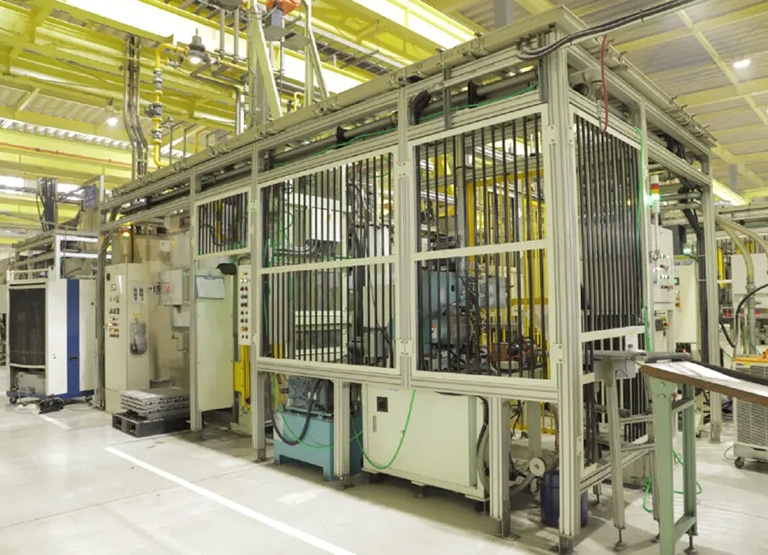
Aluminum Die Casting & Machining
High-Cost Competitiveness and Quality Product Manufacturing
We continuously strive to create high-quality products with strong cost competitiveness, allowing our customers
to entrust their aluminum die casting needs with confidence. Below are some examples of our efforts.
-
In-House Production Line Design & Manufacturing
To efficiently produce high-quality aluminum die cast parts, we design and manufacture all
production lines and auxiliary equipment in-house, always optimizing our manufacturing
processes. -
In-House Mold Design & Manufacturing
We also design and manufacture some of the molds used in our production lines, reducing lead
times and costs during the startup and troubleshooting phases. -
IoT Implementation for Monitoring Production
We have implemented IoT technology that enables us to monitor operating conditions, yield rates,
error statuses, and casting parameters at a glance, allowing for quick responses and
improvements. -
3D Measurement and CT Scanning
To ensure the high quality of our aluminum die cast parts, we have introduced 3D measurement
devices and CT scanners to inspect internal defects. -
CAE Simulation
We perform fluid analysis (CAE) to design optimal casting methods, improve quality, and reduce
costs (e.g., lightweight product designs).
The Great Potential of Aluminum Die Casting
Aluminum die casting is used in various fields, with the automotive industry being the largest market. As the
industry shifts towards electric and fuel cell vehicles (EVs and FCVs), reducing vehicle weight to extend range
and improve fuel efficiency becomes critical. Aluminum, known for its lightweight and high heat dissipation
properties, plays a key role in addressing this need. Furthermore, aluminum is highly recyclable, making it an
environmentally friendly material. At Ihara Manufacturing, we leverage the strengths of aluminum die casting to
contribute to a better society through continuous innovation.
What is Aluminum Die Casting?
Aluminum die casting involves casting products by injecting molten aluminum alloys into molds at high speed and
pressure. This method results in products that are lightweight yet strong, with high thermal and electrical
conductivity. Aluminum die cast products are widely used in automotive parts, machinery, electronics, and more.
Aluminum Die Casting Manufacturing Process
At Ihara Manufacturing, many of our processes for aluminum die cast part production are automated, ensuring both
high productivity and quality.
-
1.Aluminum Melting
Aluminum ingots and return materials are melted in a furnace.
-
2.Pouring Molten Aluminum into Casting Machines
The molten aluminum is poured into the die casting machine.
-
3.High-Speed, High-Pressure Casting
The molten aluminum is injected into the molds at high speed and pressure.
-
4.Robotic Removal
The molded aluminum die cast products are removed by robots.
-
5.Mold Release Agent Application
A release agent is applied to the mold to make it easier to remove the next casting.
-
6.Trimming
Excess material, such as runners and overflow, is removed from the cast parts.
-
7.Cooling
The products are automatically transported on cooling conveyors.
-
8.Deburring with Robots
Burrs are removed automatically using robots equipped with deburring tools.
-
9.Shot Blasting
Small metal balls are blasted at the products to remove fine burrs.
-
10.Product Inspection
Dimensional inspections are conducted as necessary, and final quality checks are performed
visually.
Advantages of Aluminum Die Casting
The reason why aluminum die casting is used in many fields is because it has many advantages. I have summarized
the benefits.
-
Lightweight
Aluminum die cast products are lightweight, making them ideal for products and parts that need to
minimize weight. -
High Strength
Despite being lightweight, aluminum die cast products offer high strength and durability.
-
Excellent Mass Production Capabilities
Once a mold is created, identical products can be mass-produced efficiently.
-
Precision in Shape
Die casting allows for precise, complex shapes, making it suitable for products requiring high
dimensional accuracy and a smooth surface finish. -
High Thermal and Electrical Conductivity
Aluminum alloys effectively conduct heat and electricity, making them suitable for engine parts and
components used in electric vehicles. -
Environmentally Friendly
Aluminum is highly recyclable without degradation in quality, making it an environmentally sustainable
material.
Disadvantages of Aluminum Die Casting
Aluminum die casting has many advantages, but it also has some disadvantages compared to other materials. I have
summarized these points.
-
Internal Quality Defects
Aluminum die cast products may have internal defects like porosity, making them less suitable for
applications requiring high pressure resistance. -
High Initial Costs
Die casting requires expensive molds, leading to high initial costs, especially for small production runs
or products with many variations. -
Limited Strength Compared to Steel
While aluminum offers many advantages, it is not as strong as steel, limiting its use in high-strength
applications. -
Low strength compared to steel etc.
While aluminum is lightweight, it has lower strength than other metal materials such as steel, so it may
not be suitable for certain applications where high strength is required.
Differences Between Die Casting and Other Casting Methods
Besides die casting, there are other methods such as sand casting, gravity casting, and low pressure casting,
each of which has different manufacturing methods, characteristics, and advantages. I have summarized the
differences between them.
Die Casting
Molten aluminum is injected into molds under high pressure, allowing for precise shapes and complex designs. It
is ideal for mass production but requires expensive molds.
Gravity Casting
Molten aluminum is poured into molds using gravity. While the process allows for better internal quality and
lower mold costs, it lacks the dimensional accuracy of die casting.
Sand Casting
A casting method using sand molds, which are less expensive than metal molds, making this method ideal for
prototypes and small runs. However, it is not suitable for mass production due to the lower surface finish and
dimensional accuracy.
Leave Your Aluminum Die Casting Needs to Us
With years of experience and a solid track record in aluminum die casting, Ihara Manufacturing offers
high-quality and cost-effective solutions to meet your needs. We handle every stage of production, from research
and development to prototyping and testing. If you are looking for a reliable partner for aluminum die cast
parts, feel free to contact us.